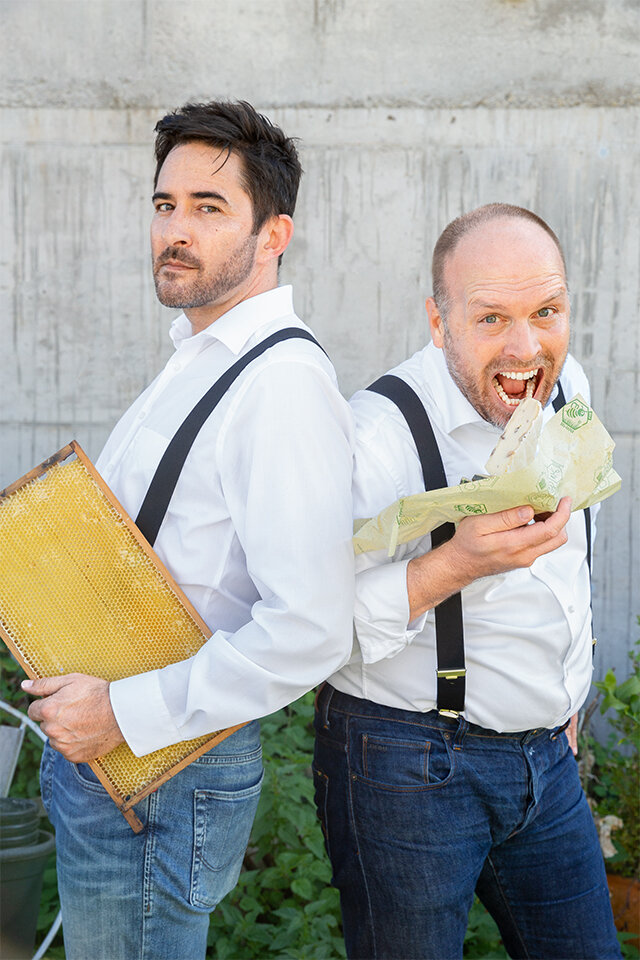
„Die Wachsschicht auf dem Papier ist dick genug, damit der Käse frisch bleibt, aber so dünn, dass sie das Kompostieren nicht verzögert oder in der Biogasanlage wie eine Bremse wirkt.“
Steffen Krötz, bee-paper
Auf der Suche nach einem Namen für ihr Start-up ließen sich die drei von einem Tippfehler inspirieren. „Wenn sie meinen Vornamen schreiben wollen, verirren sich die Leute regelmäßig auf der Tastatur“, sagt Sven Seevers. „Ich habe unzählige Mails, Briefe und sogar ein Zeugnis, in denen steht Seven Seevers.“ So entstand 2017 die Superseven GmbH. Um eine neue Einnahmequelle ging es nicht, eher im Gegenteil. Sie ließen sich ihre Experimente etwas kosten: Zeit vor allem, Geduld, Nerven, aber auch Geld.
Unter dem Markennamen Repaq entwickelte Superseven eine plastikfreie Folienverpackung aus 90 Prozent Zellulose, 5 Prozent Wasser, 4 Prozent Glyzerin, 1 Prozent Bindemittel. Der Zellstoff stammt aus Holzresten nachhaltiger Forstwirtschaft. Die Folie schließe damit einen biologischen Kreislauf, sagt Katja Seevers. „Was aus der Natur entnommen wird, soll am Ende als Wasser, CO₂ und Biomasse dahin zurückkehren.“
Lange bevor Erdöl oder Erdgas zu den gängigen Rohstoffen der Plastikindustrie wurden, nutzte man Naturstoffe wie Zellulose, um Kunststoff herzustellen. Vor gut 150 Jahren entwickelte der US-Amerikaner John Wesley Hyatt mit seinem Bruder Isaiah erstmals einen Kunststoff, der sich mit Wärme verformen ließ. Der Name: Zelluloid. Mit pflanzlicher Zellulose, Nitriersäure und Kampfer als Weichmacher ebneten die Hyatts den Weg ins Kunststoffzeitalter. Erst nach Ende des Zweiten Weltkriegs setzte die Industrie auf die fossilen Rohstoffe, die damals unschlagbar günstig waren. Seitdem fristen Biokunststoffe ein Nischendasein. „Unglaublich, dass solche Materialien einfach so in Vergessenheit geraten sind“, sagt Hannes Füting.
Die Holzfolie von Superseven lässt sich bedrucken, mit Heißsiegeln verschließen, ist resistent gegen Öle und Fette, lädt sich bei Reibung nicht elektrostatisch auf, schützt vor Feuchtigkeit und Hitze. Sie lässt sich stanzen, lasern, falten, läuft auf vielen Verpackungsmaschinen einwandfrei. „Unsere Folie sieht aus wie Folie aus Öl, sie fühlt sich auch so an, sie knistert, ist aber nicht aus einem fossilen, sondern aus einem nachwachsenden Rohstoff“, sagt Füting. „Durch sie kann kein Mikroplastik entstehen, denn sie ist plastikfrei. Und sie löst sich im Gartenkompost in 42 Tagen spurlos auf.“
Für die Albert Herz GmbH hat Superseven gerade eine Käseverpackung entwickelt, die ihre Folie aus der Nische holen könnte. Der Jahresabsatz der Käsemacher mit Sitz in Kimratshofen, mitten im Allgäu, liegt bei 14.000 Tonnen Käse. Auf dem Prototyp, den Superseven für den Bergkäse von Herz entwickelt hat, haftet durch kompostierbaren Kleber ein kompostierbares Etikett, auf dem mit kompostierbaren Farben eine Kuh gedruckt wurde, die vor einer Berglandschaft auf einer Weide liegt. Das soll Naturnähe suggerieren – im Käse und in seiner Hülle.
Die Crux ist nur: Wenn man selbst nicht so naturnah lebt und keinen Komposthaufen hat, kann man die Verpackung nicht verrotten lassen. In der Biotonne dulden die Entsorger die Holzfolie nicht. Sie lässt sich nicht von einer normalen Plastikfolie unterscheiden, die ihnen die Biogasanlage verstopfen würde. Dass die Holzfolie keine normale Folie ist, sieht man ihr nicht an. Also fliegt sie raus. „Dabei könntest du sie getrost in jede Biogasanlage packen oder in industriellen Anlagen kompostieren“, sagt Füting. Auch die Recyclingunternehmen können mit dem Plastik noch nichts anfangen, wenn ihre Sortieranlagen Holzfolie nicht zuordnen können. Und so wird die Folie aus dem Wald bislang auch hier aussortiert – und landet im Feuer.
Bienenwachs hält Bienenstöcke keimfrei
150 Kilometer vom holzfolienverpackten Bergkäse entfernt, streicht Steffen Krötz über ein Stück Papier. Es ist gelbgräulich, eine Seite rau, eine Seite glatt. Auf den ersten Blick unterscheidet es sich nicht von dem Einschlagpapier, in das ein frisch geschnittener Käse im Bioladen oder auf dem Wochenmarkt eingewickelt wird. Und trotzdem ist es anders. Krötz’ Papier wird aus Zellstoff, Grasfasern und wenig Wasser gemacht. Die beschichtete Seite ist nicht wie üblich aus Polyethylen, sondern aus Bienenwachs. Anders als Holzfolie kann das so genannte Bee-Paper zum Biomüll in die braune Tonne. „Die Wachsschicht ist dick genug, damit der Käse frisch bleibt, aber so dünn, dass sie das Kompostieren nicht verzögert oder in der Biogasanlage wie eine Bremse wirkt“, sagt Krötz.